How Upgrading to an Automated Powder Coating Machine Affects Productivity
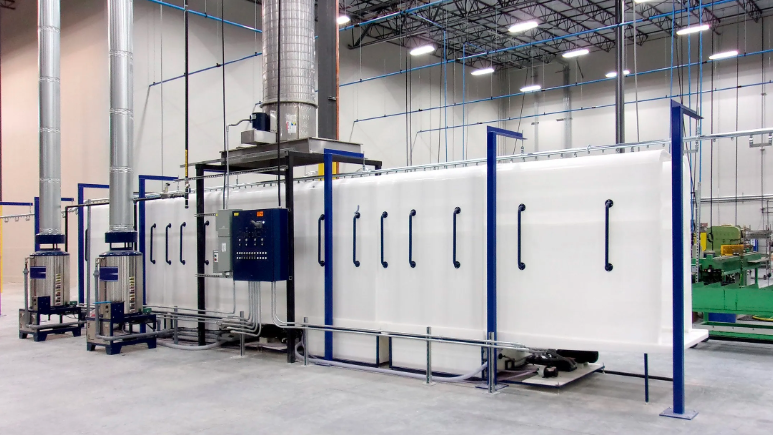
In a busy production shop, every second counts. Teams work hard to meet deadlines, hit quality standards, and keep up with rising demand. Swapping out older equipment for a modern powder coating machine can quietly transform that daily grind into a smoother, faster operation—without needing a complete overhaul.
Consistent Batch Turnaround Boosts Throughput Rates
Production lines thrive on predictability. An automated powder coating machine delivers a steady rhythm by finishing batches at the same pace every time. This removes the usual bottlenecks that slow things down in manual systems. Whether it’s parts for industrial machinery or custom hardware, consistent turnaround makes scheduling easier and allows multiple jobs to flow through in less time.
The machine’s ability to repeat the same cycle precisely ensures no surprises in drying time, coverage, or finish. This rhythm helps shops take on more work without stretching their limits. With a powder coating machine that runs on automation, teams no longer lose hours recalibrating or redoing batches. Throughput increases naturally, driven by repeatable efficiency rather than overworked staff.
Minimized Operator Intervention Accelerates Workflow
Manual systems often rely heavily on skilled technicians for nearly every task—from coating adjustments to timing and temperature. Automation shifts that responsibility to the machine, freeing up operators to oversee multiple parts of production or handle inspections. A powder coating machine with programmable settings can reduce hands-on time by a wide margin.
Instead of watching over a process for hours, an operator can now set the cycle, hit start, and move to other responsibilities. The less human intervention required, the fewer delays from fatigue or distraction. The workflow becomes faster not because people work harder, but because the system supports them with better tools.
Standardized Application Improves Resource Efficiency
In a manually operated system, it’s easy to apply too much or too little powder. That inconsistency not only wastes material but can also lead to rework or rejected parts. Automated powder coating machines are designed to apply the coating evenly, using programmed paths and spray settings. That kind of precision adds real value.
With each part receiving exactly the amount it needs—no more, no less—the shop reduces its use of powder and still ends up with better results. Resource efficiency isn’t just about saving powder; it’s about getting a dependable finish while reducing time spent fixing problems. Automation brings that level of consistency to the table.
Streamlined Powder Usage Reduces Material Costs
Every ounce of powder matters over time. Traditional setups often overspray, leaving excess powder on floors or filters. An automated powder coating machine controls spray pressure, timing, and direction, dramatically cutting back on waste. The reduction in overspray alone can lead to significant material savings over a few months.
Also, machines can recover and reuse powder in ways manual systems often can’t. Built-in reclaim systems capture extra powder and cycle it back in. This keeps material use tight and efficient, helping operations keep costs low without cutting corners on quality. It’s smarter use, not just less use.
Read also: A Critical Examination of WCPSS.Technology Games
Reliable Cycle Repeatability Cuts Downtime
Downtime is productivity’s worst enemy. Whether caused by equipment tweaks or inconsistent results, it disrupts everything. With automation, the powder coating machine repeats cycles exactly as programmed—every single time. That kind of predictability keeps the line moving.
Instead of pausing to fix uneven coverage or re-bake undercured parts, shops can trust the cycle will run cleanly. Over time, fewer interruptions mean more hours spent producing and fewer spent troubleshooting. Automation turns guesswork into reliability and that reliability protects every part of the schedule.
Reduced Manual Error Enhances Output Quality
Manual work opens the door to small mistakes—missed spots, uneven layers, or incorrect temperatures. A powder coating machine removes most of that margin for error by handling each step with machine-level precision. From temperature control to airflow to coating thickness, everything gets managed through settings, not human judgment.
This precision results in higher-quality finishes that meet spec every time. Fewer touch-ups and remakes mean fewer delays. It also builds a stronger reputation for consistent output, which matters more than ever in a competitive marketplace. Quality control becomes less reactive and more automatic.
Energy Management Features Lower Operational Costs
Modern powder coating machines come with built-in energy-saving features. These include smart heat zones, idle-time energy reductions, and insulated chambers that retain heat between batches. That means shops use less electricity without sacrificing performance.
These improvements may seem small on their own, but together they make a serious dent in utility bills. Automated machines often warm up faster, maintain heat more efficiently, and reduce wasteful run time. The result is a leaner, smarter operation that lowers costs while improving output. In today’s energy-conscious world, that’s a benefit shops can’t afford to ignore.